Land Transport Innovation Portal
What is the Land Transport Innovation Portal?
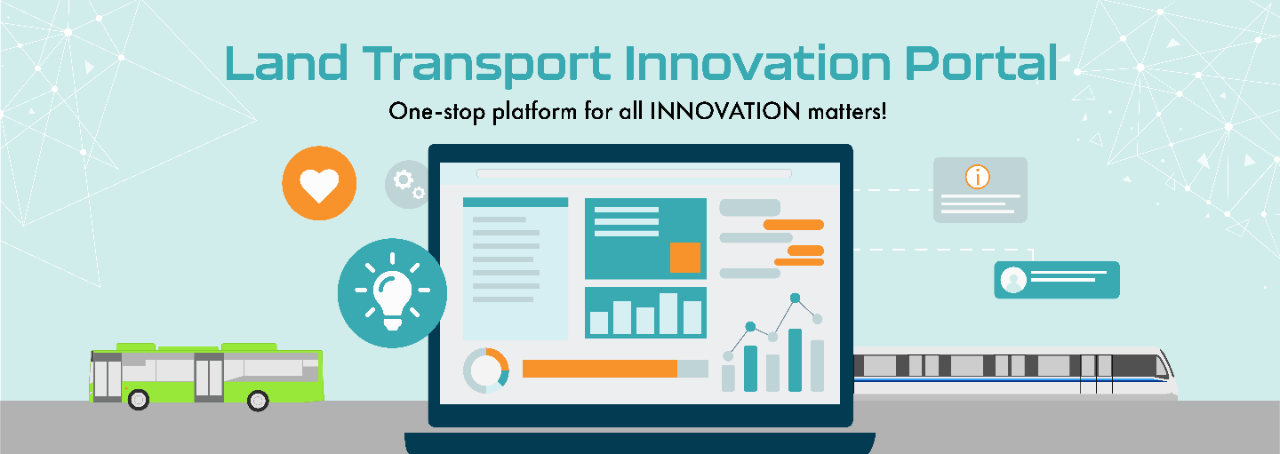
The Land Transport Innovation Portal supports the development of innovative solutions to meet the Land Transport Master Plan 2040 (LTMP 2040) goals.
Through this portal, you can:





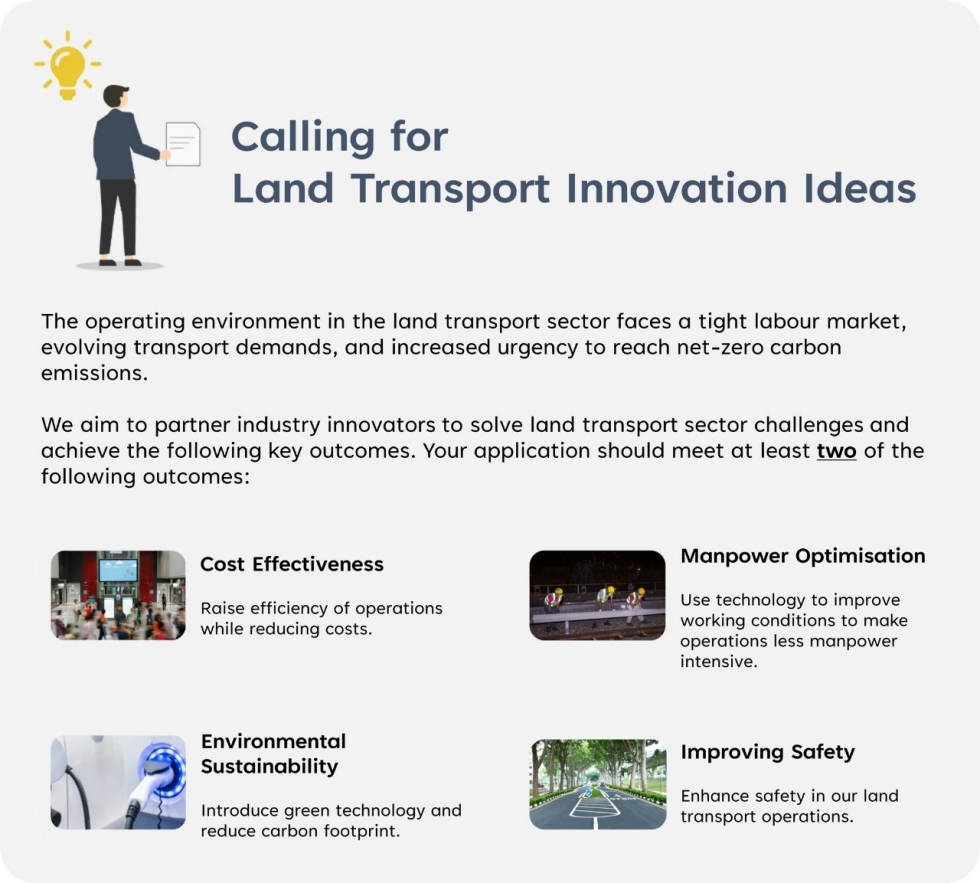
Submit your Ideas
Have an idea to help us reach our land transport goals? Submit an abstract of your proposed solution through our Submission Form. If your proposed idea matches what we are looking for, we will get in touch with you to find out more!
Who can apply?
Local and global organisations (e.g. private companies, research institutes or institutes of higher learning). Organisations should set up a base in Singapore to run the project and also own, manage and exploit rights of all intellectual property that is developed.
Proposed solutions will be evaluated broadly based on, but not limited to the following criteria:
Criteria | Description |
---|---|
Objective |
|
Innovativeness |
|
Scalability & Implementation |
|
Shortlisted solutions will be funded based on the duration, scalability and readiness of technology. Funding requirements and details will be determined based on the project.
Contact Us
Reach out to us through our Contact Form for more assistance.
Join Our Mailing List!
Join our Mailing List to receive updates on the latest land transport innovation news!
UMI Grant Call – Behaviourial Sciences in Walk-Cycle-Ride
The Land Transport Master Plan (LTMP) 2040 for Singapore envisions a land transport system where walking, cycling and riding public transport serve as the primary modes of transportation. This system is convenient and well-connected, characterised by a commuter experience that is gracious and inclusive. It also promotes a healthier lifestyle and safer journeys for all.
Encouraging desirable commuting behaviours among Singaporeans is pivotal for realising our LTMP 2040 goals. Gaining insights into Singaporeans’ perceptions, behaviours, and decision-making processes for commuting will help us to design effective policies and infrastructure. These allow us to better cater to the evolving needs of commuters.
LTA is launching a grant call to seek solutions for two problem statements, which may utilise, but are not limited to, behavioural solutions that will support the development of effective policies and infrastructure through an understanding of commuting behaviours.
(Problem Statement 1) Nexus between Transport and Health
Commuting via active mobility and public transport (Walk-Cycle-Ride) offers significant health benefits. While many have recognised the general advantages of active commuting, there's a need to quantify these benefits more effectively.
LTA is seeking proposals to encourage desirable commuting behaviours through 3 focus areas on Nexus between transport and health:
- Focus Area A: Quantification of health benefits for commuting by Walking, Cycling and Riding, for applications in Cost-Benefit-Analysis
- Focus Area B: Transformation of Physical and Mental Health Benefits Quantification from Focus Area A, into Relatable Units for Communication with the General Public
- Focus Area C: Studying the Effectiveness of Quantified Health Benefits in the Application of Behavioural Change Strategies towards Active Mobility as a Mode of Transport
Proposals submitted for this problem statement must be able to address all three focus areas above.
(Problem Statement 2) The Impact of Speed in Road Accidents - Investigating Severity, Accident Rates, Driver Reaction Times, and Age-Related Parameters in Singapore
As Singapore experiences a demographic shift toward an ageing population and increased urban density, speed limit setting policies must adapt to ensure mobility and accessibility for older individuals.
Speed plays a critical role in road safety by influencing crash severity, occurrence and overall traffic dynamics. In an ageing society, speed management must balance efficiency with the need for safer, more inclusive road environments. Overseas research indicates that lower speeds reduce both the likelihood and severity of accidents, particularly among older pedestrians and drivers as they all face unique challenges related to reaction times, vision, cognitive processing, and physical vulnerability. However, there is limited evidence on optimal speed settings in ageing communities, especially in Singapore.
LTA is seeking proposals to establish quantifiable relationships in Singapore’s context between:
- The impact of vehicle speeds and the severity of injury of all road users including pedestrians, cyclists and motorists of different age groups in an on-road accident
- The impact of vehicle speeds and the accident rates, and
- The impact of speed and drivers’ behaviour/reaction time (by age group).
The research findings should also help to better understand the international speed limit setting policy vis a vis Singapore’s through international benchmarking, which includes examining speed limit by road category and speed-safety correlations across cities with comparable demographic profiles and ageing populations.
Application Process and Submission
Applicants may choose to either submit one proposal addressing a single problem statement, or submit multiple proposals, each targeting a different problem statement within this grant call.
Proposals will be selected and evaluated based on the specific criteria of each respective problem statement. More details can be found in the respective factsheets found below.
This call is open to all R&D organisations in Singapore including publicly-funded IHLs, not-for-profit research institutions, public sector agencies, private companies, and company-affiliated research entities.
The lead Principal Investigator (PI) and Co-Lead Principal Investigator (Co-PI) are responsible for delivering the outcomes of the project and will be required to have a minimum of 9 months of residency per year in Singapore. All work should be done in Singapore, unless expressly approved by LTA.
All applications and supporting documents for the grant call must be submitted by 18 July, 5pm (SGT/GMT+8) to LTA_Innovate@lta.gov.sg. Only documents in Word, Excel and PDF formats will be accepted.
LTA will conduct a briefing to provide clarifications on the grant call on 2 June 2025 at the Land Transport Authority (LTA), if a sufficient number of registrations is received. If you are interested to attend the briefing, please register by 23 May 2025, 5pm. All registered attendees will receive a confirmation via email by 29 May 2025.
Documents for submission
- Annex C Budget Template (XLSX, 41 kB)
- Annex D Project Milestones and Deliverables (DOCX, 30 kB)
- Annex E Offline Application Package (XLSX, 31 kB)
Documents for information
- Grant Call Factsheet 1 – Nexus between Transport and Health (PDF, 169 kB)
- Grant Call Factsheet 2 – The Impact of Speed in Road Accidents (PDF, 142 kB)
- Full Proposal Guidelines (PDF, 215 kB)
- List of Non-Fundable Direct Costs (PDF, 102 kB)
- Guidelines for the Management of Research Grants (PDF, 99 kB)
- Research Grant Terms & Conditions (as of 1 Jan 2020) (PDF, 146 kB)
For further enquiries on this grant call, please email LTA_Innovate@lta.gov.sg.
Land Transport Sandboxes
LTA facilitates the development and use of new technologies which are not within the scope of current standards and regulations through a sandbox arrangement. This allows a safe environment to better understand the use, benefits, and associated risks of the new technologies within our local context. Interested applicants can check out the available thematic sandboxes to submit your innovation proposals.
Sandbox for Electric Vehicle Charging Systems (EVCS)
Currently, all Electric Vehicle Charging Systems (EVCS) used in Singapore must comply with existing standards and regulations, such as the Technical Reference 25 (TR25). Advancements in Electric Vehicles (EV) charging technology have led to an increased number of EVCS deploying new technologies which are not covered under the scope of current standards, even as we regularly update these standards.
A responsive and forward-looking regulatory approach will help facilitate the deployment and development of such innovative EVCS. To achieve this, LTA has established an EVCS sandbox framework where such systems can be trialled in a controlled environment.
Closed Applications to Sandbox
- Electric Heavy Goods Vehicle (e-HGV) Battery Charging and Swapping System (BCSS) Solutions. Awarded to PSA Corporation Ltd and a consortium comprising Strides Frontier Pte Ltd and Ecoswift Pte Ltd to trial and assess the viability of battery swapping for e-HGVs.
- Electric Vehicle Mobile Charging System (MCS) Solutions. Awarded to Power-Up Tech Pte Ltd and Beecharge Innovation Group Pte Ltd, to trial and assess the viability of mobile EV charging forelectric vehicles.
General Sandbox Enquiry Form
For general enquiries about LTA’s sandboxes, please use our online form.
Data to Support Innovation Work
Enterprises, third-party developers, researchers, and the general public can obtain information from the Land Transport DataMall. This includes:
Open Datasets
- Static Datasets comprise mostly the Geographical Information System (GIS) information available in the ESRI shape file format. LTA’s statistical monthly/annual reports available in PDF and XLS formats.
- Dynamic Datasets are updated live. They are served out via APIs which are accessible with an Account Key. This is issued only to registered DataMall subscribers.
On-Request Datasets
LTA can share other datasets on a case-by case basis. This is to address requesters’ needs, while meeting LTA’s commitment to data confidentiality and privacy.
The datasets available are listed in DataMall’s “On-Request Datasets” tab. More specific information can be found within metadata in each dataset.
Two new on-request datasets are uploaded on the DataMall:
- Taxi Movement Data
- Traffic Lights Traffic Plans
To request data, requestors should download and complete the Data Sharing Form and submit it via the Contact Us page on DataMall.
Innovation @ LTA
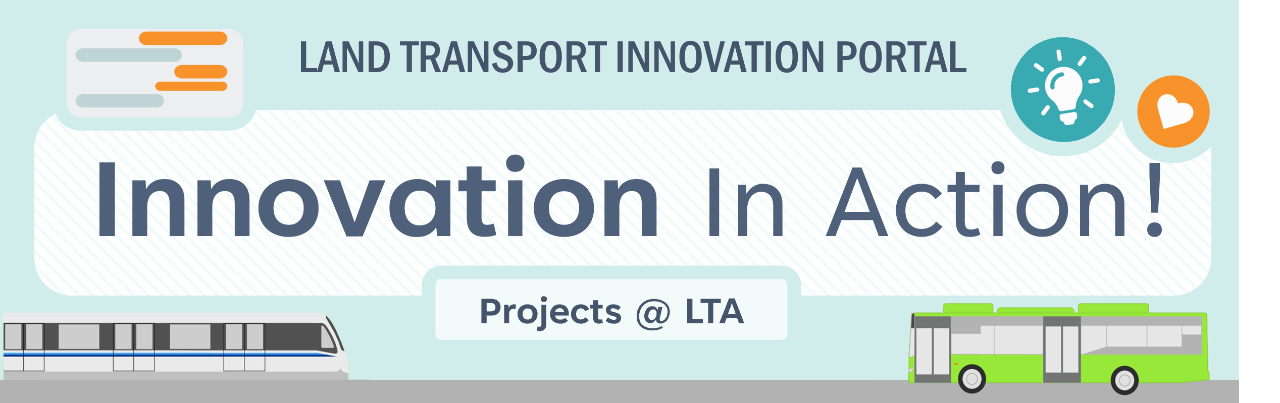
We are able to bring innovative ideas to life thanks to collaborations with industry and research partners! We aim to deliver a safe, reliable, inclusive, cost efficient and environmentally-sustainable land transport system for our commuters.
For example, did you know we are upcycling waste by using waste plastics to pave roads? This is possible with the partnership from Samwoh Innovation Centre, Singapore Polytechnic, and Contec Fiber AG.
Read the article - "Paving the Way for Eco-Friendly Roads" to find out more about this initiative.
Enhancement of Roadworks Application Process using Artificial Intelligence
- Industry Partner: NCS Pte. Ltd.
- LTA User: Road Works Regulation and Licensing Division (RWRL)
On average, there are about 200 to 300 roadworks each day, for installations and upgrading works relating to water, sewer, drainage, power and telecommunication networks. For each roadwork, the agency or private contractor must get a permit via LTA’s Permit for Road Occupation Management Portal (LTA.PROMPT) online portal.
Innovating to Improve Efficiency
To smoothen the process of roadwork applications, we worked with NCS Pte Ltd to introduce the following:
- Automatic generation of Traffic Control Plans (TCP).
- Optical Character Recognition (OCR) to check scanned documents. Applicants are alerted if anything is missing.
- Artificial Intelligence (AI) to review applications and provide recommendations for quicker processing.
A Simpler and Shorter Process
With these features, submitting applications on roads with a simple configuration is more streamlined.
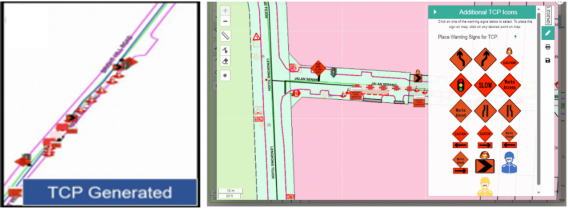
Generation of TCPs via AI/ML enhancement system
The Road Ahead
We are now exploring how to introduce more complex traffic layouts and road infrastructure. This will cater to different road configurations and traffic volume.
Viaduct Bearing Inspection with Drones
- Research Partner: Singapore University of Technology and Design (SUTD)
- LTA User: Asset Engineering (Infrastructure) Division (AEINF)
There are over 17,000 viaduct bearings along the North-South-East-West Line (NSEWL). In accordance to LTA’s Code of Practice, these must be inspected every 5 years - a process which is currently performed manually. Besides checking the viaduct bearings’ general condition, we also inspect key parameters such as longitudinal displacement and bearing rotations.
The challenges we face:
- Accessibility: Bearings are not easy to reach. They are typically elevated at a height of six metres or more, and found within small cavity spaces or above water bodies.
- Technology limitations: Current commercial-off-the-shelf drones are too large to fly close to the bearings and cannot capture close-up images in low-light. Instead, we would need to use scaffolds, cherry-pickers, and other specialised equipment to reach the bearings.
- Human error: The work is manually done by people. This can result in parallax errors and inconsistency.
Helping Viaduct Bearing Inspection Take Flight
We approached Singapore University of Technology and Design (SUTD) to develop a drone to meet our inspection needs.
They designed a lightweight mini-drone not exceeding 230mm in length, that can connects to a ground power unit via a tethered-line. Components are encased within the drone’s body so the pilot can fly it to different heights and access small cavity spaces. This eliminates the need for elaborate setups for workers to manually inspect each bearing.
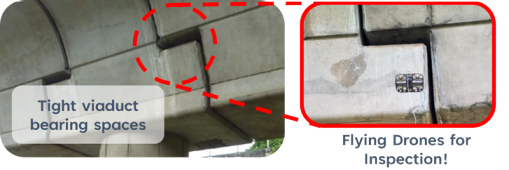
Automatic and Accurate Measurements
At each location, the drone will take high-definition images covering the entire width of the bearing and a 3D image will be generated. An automatic AI-enabled displacement extraction framework will be run to extract critical infrastructure measurements. This ensures accuracy of the inspection.
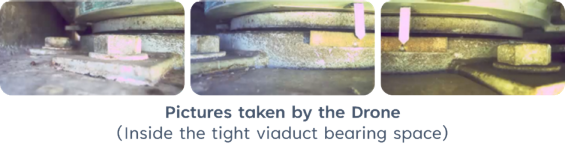
Reaching New Heights
The drone system will be used at viaduct bearing inspections for the NSEWL. It seeks to:
- Reduce the time taken to inspect each bearing from one hour to fifteen minutes
- Eliminate work-at-height risks and cumbersome logistical setups
- Allow for inspections to be done both during the day and night
- Improve accuracy and consistency of required measurements
- Overcome accessibility issues
We are exploring if the same drone system can be used in other areas such as ceiling inspections at MRT stations and road bridges.
Redesigning Temporary Bus Shelters
- Industry Partner: Shincon Industrial
- LTA User: Commuter Infrastructure Construction Division
As LTA progressively conducts upgrading works to existing infrastructures, it is necessary to put in place temporary structures while undergoing upgrading works. This includes the construction of temporary bus shelters.
These temporary shelters require permits such as BCA Temporary Build Permit (TBP) and Permit to Use (PTU), before any site work can commence. A two-week construction period followed by another two weeks for the demolition process would also be required.
Incorporating Innovation to an Existing Design
A conventional temporary bus shelter requires safety bollards and roof panels to be installed.
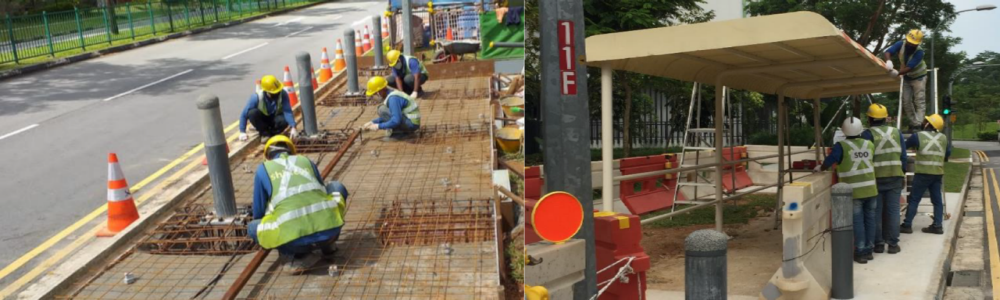
Bollard footing (left) and roof panel installation (right) for conventional temporary bus shelters
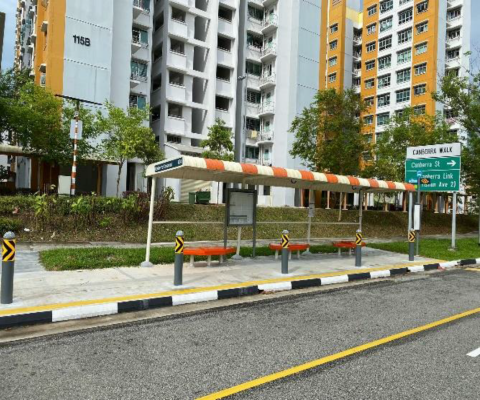
Finished Temporary Bus Shelter
To reduce the time needed and streamline the manpower-intensive construction process, LTA took an alternative approach to the form and design of the temporary bus shelter. Bollards are replaced with concrete barriers and the roofing is replaced with a canvas.
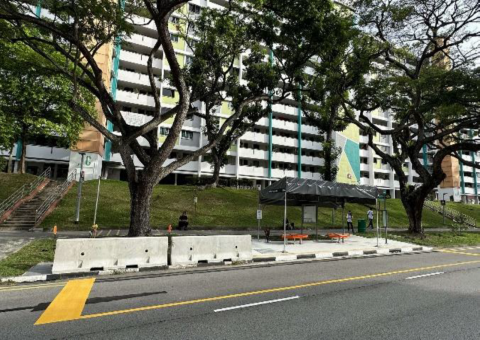
Redesigned Temporary Bus Shelter
LTA engineers worked closely with the contractors/suppliers to ensure that the redesigned temporary bus shelter does not compromise commuter safety and experience. It is also able to withstand inclement weather, as evident throughout a trial conducted from October 2022 to December 2023.
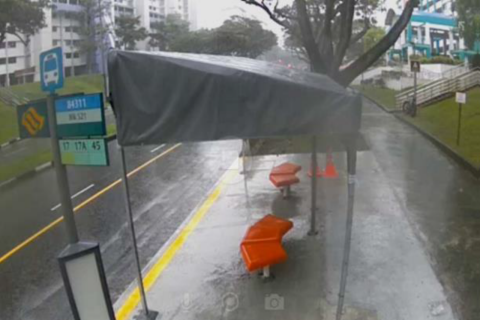
Redesigned Temporary Bus Shelter in Adverse Weather Conditions
Transforming Into Real Benefits
Overall, LTA is now able to reduce the man-hours required to install the redesigned temporary bus shelter by 75% and shorten the installation and removal durations from one month to one week. Due to the large number of bus shelters to be upgraded, the time and cost savings acquired in the construction process will be compounded significantly.
Commuters can also enjoy the upgraded bus shelters sooner, with minimised construction inconvenience (noise or dust) due to the more efficient construction process.
Redesigning the Future
Beyond bus stop upgrading works, LTA is also exploring the usage of the redesigned temporary shelters for simple maintenance works, short term road diversion and minor improvement works that would only require the diversion or closure of bus stops for a short duration.
Enhancing Utilities Visualisation in Construction Works with Augmented Reality (AR)
- Industry Partner: Gammon Bachy Soletanche Joint Venture
- LTA User: Cross Island Line CR116 (CRL AMK Station) Project Team
Excavation works carried out during construction operations entail inherent risks as underground utilities are not visible from the surface. Any unexpected incident from excavation causing damage to underground utilities could result in major service disruptions.
To investigate and verify the location of existing utilities, trial trenches are typically carried out prior to excavation works to identify the details of the underground utilities, such as the type, depth and width of utilities. Information from the trial trenches is then consolidated into a 2D utility layout plan as a reference.
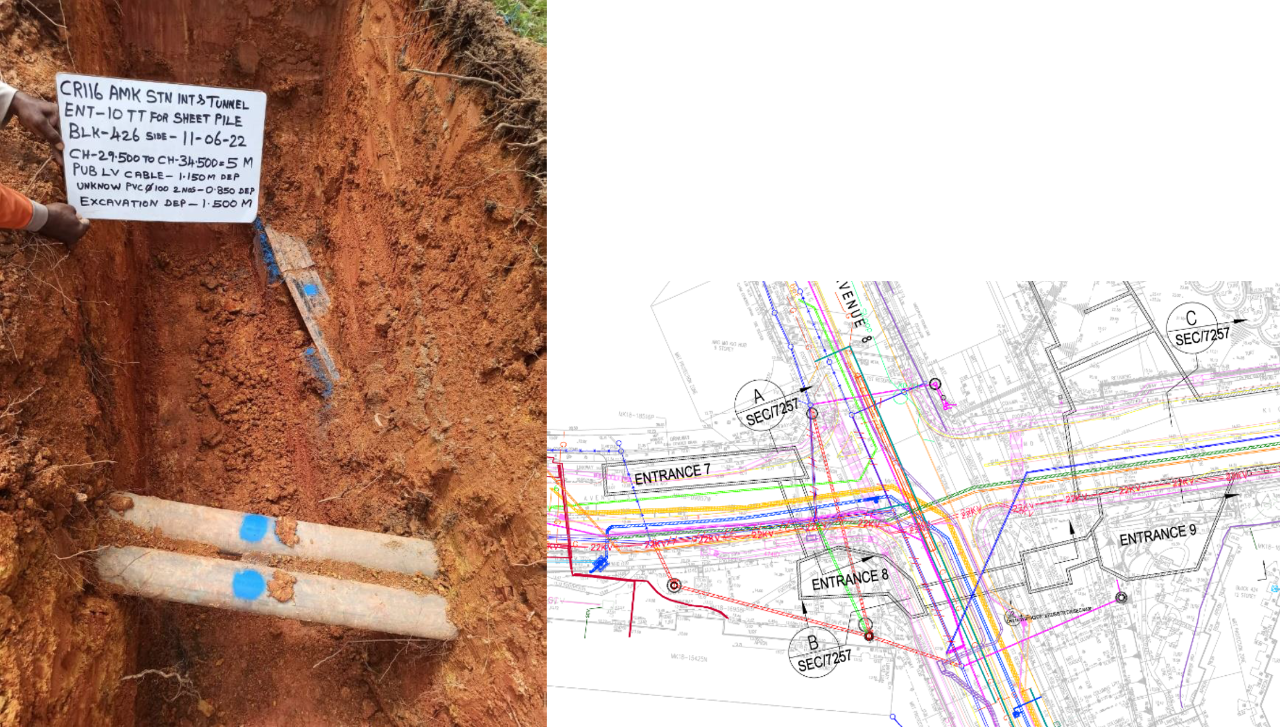
Image of a trial trench (left) and 2D utility layout plan (right)
Upon verifying the details of the utilities, physical utility markers are used to mark out the location of existing underground utilities. However, there are still limitations to this method of identifying utilities, such as:
- Utility markers may be tampered with, or accidentally shifted;
- Critical information, such as utility alignment, is not clearly displayed;
- Clustering of utility markers within the same area may cause confusion; and
- Utility markers are unable to be installed directly on footpaths and carriageways.
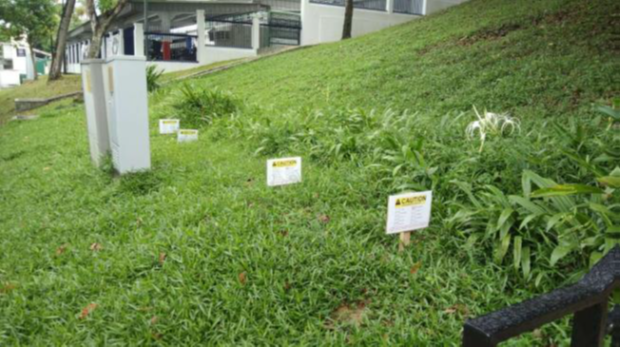
Image of typical physical utility markers on site
Using Augmented Reality (AR) to Aid Visualisation of Underground Services
To aid the visualisation of underground utilities, LTA explored and adopted the use of Augmented Reality (AR) technology for more efficient identification of utilities on site.
Using the Augmented Visualisation of Underground Services (AVUS) system, the 3D Building Information Modelling (BIM) that was developed from the 2D layout plan, can be uploaded and viewed on site via AR using any mobile device (e.g. smartphones or tablets). This provides convenient access with centimetric accuracy, allowing easy viewing of the utility alignment on site, as compared to conventional physical utility markers. AVUS also provides easier reference of utilities’ key parameters.
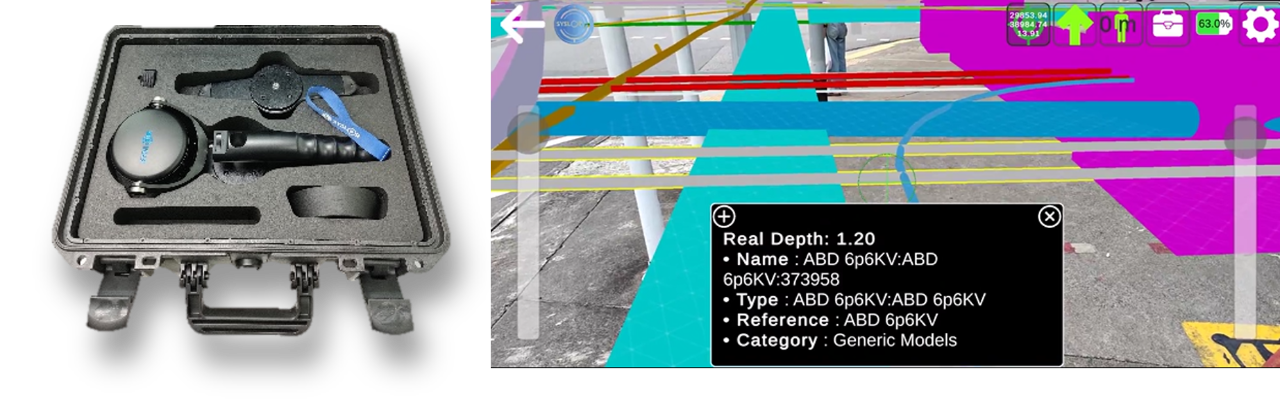
Image of the AVUS antenna (left) and AR visualisation of utility on site (right)
The AVUS offers several benefits over the conventional method to:
- Alleviate the reliance on typical utility markers installed on site above ground (these have inherent limitations that likely present inaccuracies);
- Easier referencing of the utilities against landmarks on site; and
- Clearer identification of utilities information such as type and depth of utility.
AI-Powered Road Maintenance with Mobile Geotagging
LTA conducts regular inspection of road infrastructures across Singapore in order to ensure motorists’ and public safety, to pick up any defects that can be repaired in a timely manner so that Singapore’s road infrastructure is functional and safe for use at all times.
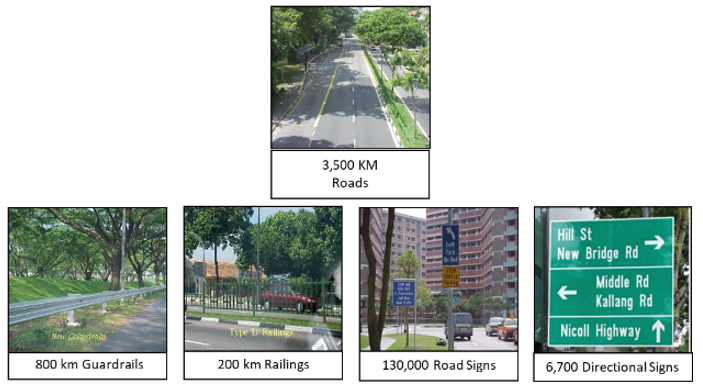
Examples of Road-Related Facilities
The process is labour-intensive, which requires the inspectors to drive through, manually pick up and record defects and generate manual reports.
The heavy reliance on manual effort and labour was further highlighted and challenged during the Covid-19 pandemic. In addition, the defects picked up were heavily subjected to inspectors’ judgement, knowledge and experience, which led to discrepancies and inconsistencies in defect capturing and reporting.
LTA also leverages on FormSG to collect information and data on active mobility enforcement and road defects. This supplements any gaps in pothole detection that manual inspections may have missed.
However, FormSG is not equipped with geotagging capabilities. Without this capability, the process involved manually identifying locations on Google Maps and transferring the coordinates to FormSG fields. This proved to be time-consuming and inefficient to switch between applications and transfer long numerical values.

Manual Geocoding of location points via Addresses
Making use of New Technology Tools
To explore the viability of adopting new technologies into the road inspection process, the team conducted a proof-of-concept to test the existing digital and technological solutions in the market. It was then evaluated that Artificial Intelligence and Video Analytics (AI/VA) solutions can provide a more cost-efficient, adaptable, and practical way of automated defect detection and reporting, enabling enhanced operational efficiency in our road inspection process.
Using an open-source map engine, GeoFormSG was built to integrate the existing functionalities of FormSG to enable geotagging, resulting in high and widespread impact to operations, with relatively low implementation effort.
GeoFormSG is an internet-enabled website built on top of any FormSG form, allowing users to attach location tags to specific points on a map. On GeoFormSG, users can either pinpoint their location on a map or input an address to obtain corresponding longitude and latitude values. Subsequently with just one click, users are redirected to their FormSG where the geotagged data is automatically captured into the respective fields in the form.
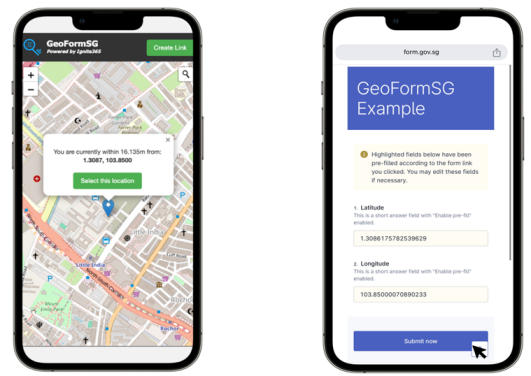
(Left) Screenshot of GeoFormSG App with user's current location detected via GPS
(Right) Screenshot of automatic pre-filling of selected coordinates in FormSG
Reaching New Productivity Gains
LTA has been adopting this nationwide since July 2023. Through this new AI/VA inspection method, we have achieved:
- Productivity gain of 60% through digitalisation and automation of the road inspection and end-to-end reporting process,
- Higher accuracy of defect detection to more than 85%, while improving the coverage of the types of defects, and
- Reduction by 60% in reliance on manual inspection labour and number of inspection vehicles required.
GeoFormSG has similarly produced productivity gains, cutting down the time needed for geotagging by 60%.
Other than time savings, data points in coordinate form are not only useful for pinpointing locations but for downstream data analysis to generate visualisations on the recorded feedback. GeoFormSG ensures good clean data captured right at the source, laying the foundation for insightful data analysis.